Mission:Zero
Thinking ahead: from decarbonization to circular production
Audi set the goal to achieve net carbonneutrality1 by 2050 at the latest. The brand with the four rings has already implemented various measures along the entire value chain to support this goal. All Audi production sites worldwide have had net carbon-neutral operations since 2025. Audi uses the term “360factory” to describe its comprehensive strategy for developing a future-oriented and sustainable production network. Audi's environmental program, Mission:Zero, is a crucial element of the strategy. Audi is using it to consolidate all measures to reduce its ecological footprint in production and logistics. The program goes beyond decarbonization and addresses also the key areas of activity: sustainable water use, resource efficiency, and protecting and preserving biodiversity. The company’s vision is to establish circular production where resources such as plastics, water, and other raw materials are in closed cycles.
Since the beginning of 2025, all Audi production sites worldwide have been manufacturing under net carbon-neutral conditions. The former Audi production site in Brussels made the start in 2018, with Audi Hungaria and the Böllinger Höfe sports car production facility following suit in 2020. The main Audi plant in Ingolstadt reached this important milestone at the beginning of 2024. The final steps necessary to achieve net carbon-neutral production at all Audi sites globally were then taken in Neckarsulm and San José Chiapa (Mexico). In the important Chinese market, Audi and its Chinese partner FAW started production of fully electric models at a newly built plant in Changchun at the end of 2024. The plant will be the first site for Audi models in China to aim for net carbon-neutral production. The Audi environmental program Mission:Zero also provides the framework for holistic sustainable production at that location.
A 360-degree approach toward the production of the future
Net carbon-neutral production and all other goals of the Mission:Zero environmental program contribute to the overarching 360factory strategy, which is guiding Audi on its path towards the production of the future. The goal is the modernization, digitalization, and transformation of existing Audi plants. With the 360factory, Audi can achieve even greater flexibility and efficiency in production without sealing additional areas for new buildings. The strategy follows a 360-degree approach that harmonizes the various perspectives in production – from the needs of customers and the requirements of society to the interests of employees and stakeholders.
The company uses four target dimensions to benchmark the strategy: profitability, sustainability, attractiveness, and flexibility. Every measure that Audi implements contributes to at least one of these goals.
One particular challenge is integrating renewable energies into the established infrastructures at Audi’s sites. For example, the company is stepping up the use of photovoltaic systems and increasing the proportion of heat supplied from its renewable sources. Audi is pursuing a hotspot-based approach to water use, focusing on areas where availability is critical or demand is exceptionally high. For example, water is a priority at the San José Chiapa site in Mexico since water is a rare commodity there as it is.
Comprising of experts from all sites, the Mission:Zero team members are in close contact throughout the company. Together, they identify where there is a particular need for action, which sites will serve as the benchmark in individual areas, and which solutions can be applied at other sites. Pilot projects allow the team to test the effectiveness and feasibility of the solutions and to transfer the findings.
Climate-friendly transport logistics and sustainable packaging
Audi’s logistics processes make a significant contribution to the company's sustainability. This means the company can also systematically reduce emissions outside the plant gates. As early as 2010, Audi was the first company to use “green trains” that run on green power. The premium car manufacturer partners with the transport and logistics company DB Cargo to operate net carbon-neutral rail logistics – within Germany, rail logistics is entirely carbon-free. The brand with the four rings aims to continuously increase the share of rail freight in inbound logistics. Audi uses new loading and unloading concepts to make rail transport more efficient while leveraging the flexibility of alternative trucking technologies for pre-carriage and onward carriage. Since April 2024, Audideploys the first CT block train for the Ingolstadt, Neckarsulm, and Győr locations; it can operate this kind of train independently of modern rail infrastructure such as terminals and stations. The acronym CT stands for combined transport and is a mode of transport by which goods are primarily transported by rail; biogas trucks are used for pre-carriage and onward carriage, which results in carbon emission savings of up to 80 percent.
Overseas transport provides the greatest lever for decarbonization in finished vehicle logistics. Audi works closely with Volkswagen Group Logistics in this area and increasingly relies on alternative drive systems, such as ships that run on environmentally friendly liquefied natural gas (LNG).
As another measure in logistics, Audi is strategically and sustainably optimizing packaging at all locations for resource efficiency. As a general rule, the company avoids packaging whenever possible. Wherever packaging material is necessary, Audi uses circular and renewable raw materials. Starting in 2030, the proportion of circular materials in packaging for new vehicle projects will increase to more than 90 percent.
To this end, Audi factors in sustainable and resource-efficient packaging concepts from the early planning phase of new vehicle projects. In holistically optimizing these concepts, Audi incorporates requirements into supplier specifications. This approach has allowed the brand with the four rings to conserve more than 650 tons of plastic annually since 2020, including over 120 tons of polystyrene and foam packaging.
Four-pillar concept for net carbon neutrality in Ingolstadt
Audi’s logistics processes make a significant contribution to the company's sustainability. This means the company can also systematically reduce emissions outside the plant gates. As early as 2010, Audi was the first company to use “green trains” that run on green power. The premium car manufacturer partners with the transport and logistics company DB Cargo to operate net carbon-neutral rail logistics – within Germany, rail logistics is entirely carbon-free. The brand with the four rings aims to continuously increase the share of rail freight in inbound logistics. Audi uses new loading and unloading concepts to make rail transport more efficient while leveraging the flexibility of alternative trucking technologies for pre-carriage and onward carriage. Since April 2024, Audideploys the first CT block train for the Ingolstadt, Neckarsulm, and Győr locations; it can operate this kind of train independently of modern rail infrastructure such as terminals and stations. The acronym CT stands for combined transport and is a mode of transport by which goods are primarily transported by rail; biogas trucks are used for pre-carriage and onward carriage, which results in carbon emission savings of up to 80 percent.
Overseas transport provides the greatest lever for decarbonization in finished vehicle logistics. Audi works closely with Volkswagen Group Logistics in this area and increasingly relies on alternative drive systems, such as ships that run on environmentally friendly liquefied natural gas (LNG).
As another measure in logistics, Audi is strategically and sustainably optimizing packaging at all locations for resource efficiency. As a general rule, the company avoids packaging whenever possible. Wherever packaging material is necessary, Audi uses circular and renewable raw materials. Starting in 2030, the proportion of circular materials in packaging for new vehicle projects will increase to more than 90 percent.
To this end, Audi factors in sustainable and resource-efficient packaging concepts from the early planning phase of new vehicle projects. In holistically optimizing these concepts, Audi incorporates requirements into supplier specifications. This approach has allowed the brand with the four rings to conserve more than 650 tons of plastic annually since 2020, including over 120 tons of polystyrene and foam packaging.
The Győr site: Hungary’s biggest consumer of industrial geothermal energy
A major step for Audi Hungaria toward carbon neutrality was the transition to green power, which was accomplished through, among other things, the commissioning of Europe’s largest rooftop photovoltaic system, covering an area of around 160,000 square meters. The system reaches a maximum power of 12 megawatts. The company also uses geothermal energy as a heat supply, having met more than 70 percent of its heat requirements with renewable geothermal energy since 2015. This makes Audi Hungaria the biggest consumer of geothermal energy in the country. The system provides the Győr site with at least 82,000 megawatt hours of heat energy each year.
Audi Hungaria covers its remaining heat requirements with biomethane certificates. Carbon emissions that are currently unavoidable – from engine test stands, for instance, are compensated with internationally recognized and certified climate protection projects, which counteract around five percent of carbon emissions. Moreover, the company uses climate-neutral “green trains” in its logistics processes and, in common with all other locations, introduced a closed cycle for recycling secondary aluminum, the Aluminum Closed Loop, in 2020.
Measures for the conscious and sparing use of water
Audi relies on efficient processes, closed water loops, optimized use of rainwater, and reduced pollution loads to use water consciously and sparingly. In 2023, Audi became the first premium car manufacturer to join the Alliance for Water Stewardship (AWS). Gerd Walker, Member of the Board of Management for Production and Logistics at AUDI AG, says: “We want to significantly reduce our use of fresh water and cut our environmentally weighted water consumption in half by 2035. To do that, we’re already using recycled water, which is used repeatedly and reprocessed within the loop wherever possible. Our vision is to have closed water cycles at all our production locations.”
A new water supply system is currently being built at the Neckarsulm site. When it goes into operation in the course of 2026, the process water for the entire plant will be managed in a circular system, saving more than 70 percent of fresh water. To do this, Audi is relying on a closed water cycle with the wastewater treatment plant of the Abwasserzweckverband Unteres Sulmtal, which is adjacent to the plant. Audi will use filter systems and membranes to further treat the water purified by the wastewater treatment plant for production. The used process water will then flow back into the wastewater treatment plant.
A service water supply center has been used at the Ingolstadt site since 2019. Together with the previous treatment system, roughly half of the wastewater generated is fed into a cycle where it is treated and processed for reuse.
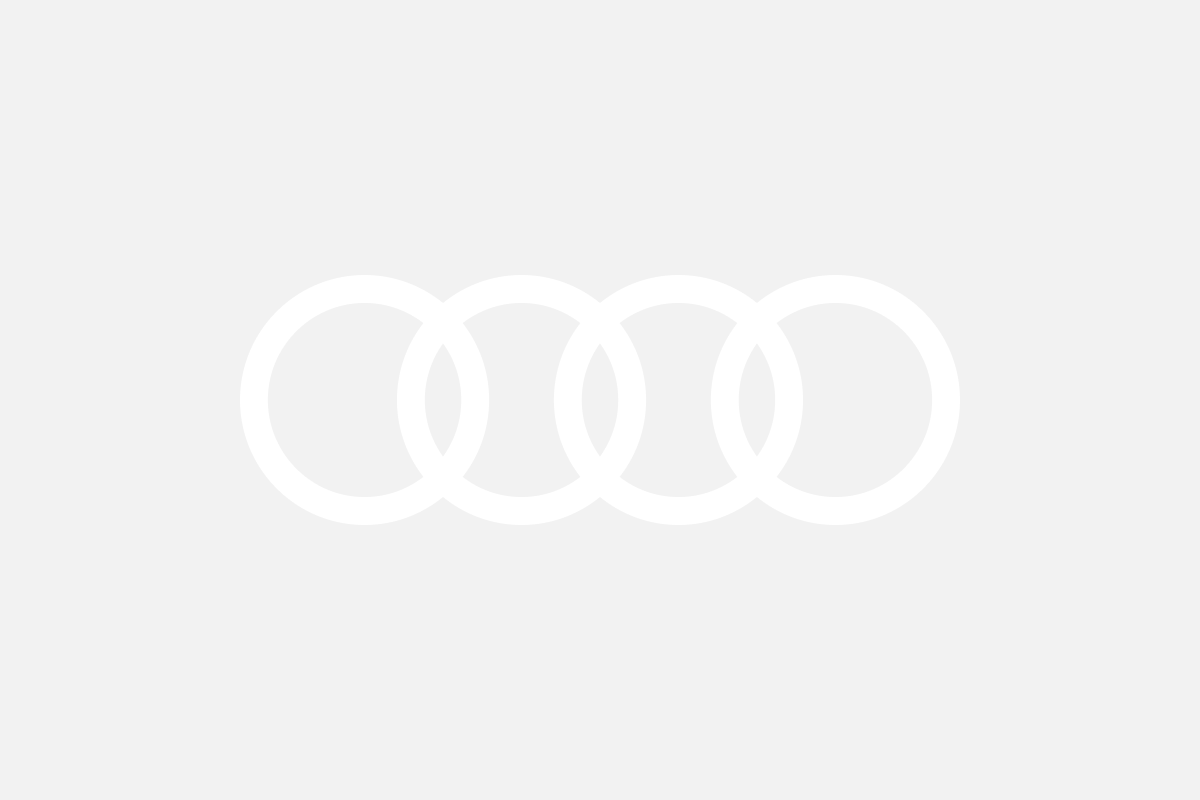
Pioneer Audi México achieves AWS certification
Using water sparingly is very important, especially in a drought-prone country like Mexico. For this reason, Audi México is leading by example: In late 2023, the San José Chiapa site became the world’s first automotive plant to have its sustainable water management system certified by the Alliance for Water Stewardship (AWS). The international AWS standard helps companies assume responsibility beyond their factory gates and use water as efficiently as possible while considering all relevant stakeholders.
In 2018, Audi México became the world’s first premium manufacturer to produce cars completely wastewater-free. In 2014, a rainwater reservoir with a retention capacity of 234,000 cubic meters was constructed on the plant site in San José Chiapa as a vital long-term measure to protect scarce natural resources. During the six-month rainy season from May to October, the reservoir fills with rainfall, which is then treated and used in the plant.
The water used in production goes through a multistage treatment process on-site, depending on the level of contamination. For example, wastewater generated in the paint shop is pretreated in a chemical-physical plant. Then, this pretreated partial stream is further treated with the rest of the site’s wastewater.
In 2015, a biological wastewater treatment plant with a daily capacity of 1,800 cubic meters went into operation in Mexico. Here, organic wastewater components are broken down by bacteria in an aerobic process. Pretreated water from the painting process also passes through this plant. In addition to biological water treatment, a reverse osmosis plant with an annual capacity of 320,000 cubic meters was built in 2018. The plant returned 130,000 cubic meters, or 130 million liters of water, to production in just over two years.
Technology park as a leading example of resource efficiency
The incampus technology park south of Ingolstadt is a leading example of resource efficiency. IN-Campus GmbH, a joint venture between the city of Ingolstadt and AUDI AG, remediated a 75-hectare former refinery on the site, using state-of-the-art processes to counteract the damage caused there.
Fifteen hectares of the total area, designated as a nature and landscape compensation area, are now beginning to thrive with a natural alluvial forest with fallow grassland and willow trees. The main site branch is home to the new Vehicle Safety Center and an Audi IT Center. It is also home to CARIAD’s largest tech hub, Volkswagen Group’s software company.
In the future, thanks to an innovative energy supply concept, incampus will be able to generate as much renewable energy as it consumes. The concept relies on waste heat recovery, energy storage, and smart control systems, among other measures, to establish a zero-energy campus. The modular energy concept is based on three basic building blocks: a water-based pipeline system, reversible heat pumps, and a cross-energy concept.
More sustainable thanks to circular production
In its commitment to resource efficiency, Audi strives to create a circular economy where resources such as plastics, water, and other raw materials are used in closed cycles. For example, Audi’s Aluminum Closed Loop has saved significant amounts of raw materials and carbon emissions. The project was first rolled out in Neckarsulm in 2017 and has since been introduced to all global locations. It works by collecting single-variety aluminum waste from production and bringing it to a supplier company that processes the waste into new aluminum coils of the same original quality before returning them to Audi.
With its joint project MaterialLoop, the brand with the four rings is researching how to close material cycles in the automotive industry. Together with 15 partners from the research, recycling, and supplier sectors, Audi is exploring reusing so-called post-consumer materials from end-of-life customer vehicles for new motor vehicle production. For example, recycled steel can be used to build new cars.
Biodiversity as a key area of activity
In addition to decarbonization, water use, and resource efficiency, biodiversity is one of Mission:Zero’s four key areas of activity. Audi is aware of the automotive industry’s responsibility for protecting biodiversity and supports the UN’s biodiversity targets; the UN has designated the decade from 2021 to 2030 a time for restoring the world’s ecosystems. Moreover, the brand with the four rings has joined the Biodiversity in Good Company initiative and is implementing biodiversity projects at all its locations.
The natural open spaces at the manufacturing site in Münchsmünster constitute a lighthouse project. Thanks to targeted ecological design, the complex near Ingolstadt offers a particularly valuable habitat for numerous species of plants and animals. At the production facilities in Münchsmünster, Audi has transformed 17 hectares of land into natural habitats for animals and plants. So far, more than 160 species of plants have flourished there, and around 100 species of wild bees have become established.
To take a strategic approach to protecting biodiversity, Audi has developed a biodiversity index analogous to its decarbonization index. The index lets Audi use special key figures to evaluate each location and define binding targets. This makes it possible for Audi to determine how biodiverse the sites are, develop a strategy for improving their natural balance, and benchmark its success.
As of: March 2025
1 Audi understands net-zero carbon emissions to mean a situation in which, after other possible reduction measures have been exhausted, the company offsets the carbon emitted by Audi’s products or activities and/or the carbon emissions that currently cannot be avoided in the supply chain, manufacturing, and recycling of Audi vehicles through voluntary offsetting projects carried out worldwide. In this context, carbon emissions generated during a vehicle’s utilization stage, i.e. from the moment it is delivered to the customer, are not taken into account.